
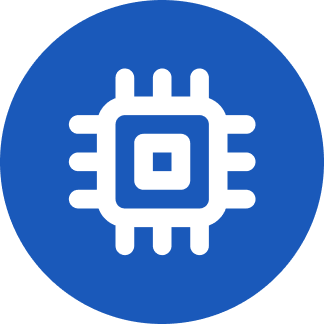
Yeah, I did ak3 month first, then 6 month, then 12 month. If you do a family plan, I think you can also get the cheaper price with a shorter lock-in.
Yeah, I did ak3 month first, then 6 month, then 12 month. If you do a family plan, I think you can also get the cheaper price with a shorter lock-in.
I get cheaper on Mint because I get the 6 or 12 month price, but it means you have to have the money up front to pay for it.
It’s all with respect to humans. Humans aren’t making the bird nests, so they’re natural, not man-made. Our houses don’t over naturally, we build them.
From the bird’s perspective, sure, nests might be bird-made and humans are part of nature. But at humans, we’ve also done a ton to shape the world and separate ourselves from nature. If your house were a fire-heated lean-to in the woods, there might be less a distinction between it and “out in nature,” but if you’re living in a city or town, your immediate surroundings probably have been heavily constructed and modified by humans.
When we were looking to buy a house, I basically crossed off the list anywhere that I couldn’t walk to at least some essentials, like basic groceries, pharmacy, a couple restaurants. Our new neighborhood isn’t nearly as walkable as where we used to rent, but everyone else heae seemed to have the same thoughts, and it’s too expensive to buy a house there.
Well, they didn’t put carpet on the bathroom floor. But they’ve arguably found something far worse.
--force-with-lease
See, It’s all safe now!
(/s, but I did royally screw up my own feature branch with a janked rebase off the main branch before though.)
The further you go, the more specialized it gets. There are people I know doing their PhDs in CS, but it was pretty much just straight math. I’m now an expert in a very specific area of robotics. But it’s only worth it if you have a specific reason to go to grad school, like for a particular career path. If it’s just because you like learning, it’s not worth it. There’s a big opportunity cost.
My older sibling did something similar - getting Ubuntu installed on my very first laptop (a 9" netbook) back in 2008 and replacing windows XP. But be warned: it is a slippery slope. At the time , I just wanted a computer that I could take class notes on (high school), and never wanted to touch programming or the terminal. Now I have a PhD in computer science. I still don’t use Arch though.
And for me, as one of the few women in my CS program: plenty of opportunities, and plenty of douchebags.
These ads are getting so much more prevalent, and so much more subtly marked. Google (and places like reddit and Facebook) designs them to feel as much like organic content as possible. I have a pihole on my home network, in part to prevent exactly the type of mistake you described.
Oh boy, I keep a page just for this!.
I need to update it (for example, Arachne perimeters in PrusaSlicer now let you print extra thin perimeters), but it’s useful to have a reference for common tolerances/dimensions like screw holes.
But a couple of my little additional pet peeves:
Personally, I don’t use 3 perimeters on most of my prints. On my prusa, they look totally fine with 2 perimeters. I only switch to 3 if I need the strength (which also almost always means I’m printing in PETG, rather than PLA, FWIW).
It is possible to get transition care while on Medicaid in some states, at least. Because it’s healthcare! So that would qualify at “taxpayer funded.” I know some states explicitly ban it, and not sure what Medicare covers. There are also government employees who can get transition care through their insurance, so could be considered taxpayer funded?
In any case, I’d much rather have all trans people be able to get taxpayer funded transition related care.
Why don’t they? Because they know it’s not true. They know that they don’t have evidence that they can present in court, and even they aren’t dumb enough to perjur themselves. Their plan was never to win in a court of law: it was so win in a court of their own supporters’ public opinion.
My house is a fixer-upper, so usually house projects. Yard work, hanging shakes, painting. It’s nice to do something physical where I can see a benefit at the end of it, when I spend my day sitting at a desk inside. It’s also nice when the neighbors compliment our progress!
I’m also team onshape. I have a powerful desktop, but I still end up doing CAD from the couch on my 6-year-old Chromebook, so onshape is a champ for that. It’s also nice for collaborating, which I do when working on bigger projects with my fiancee.
I got started with it entirely from the tutorials provided by Onshape itself. The learning curve was a lot less steep than I expected.
Video evidence showing them hiding evidence seems like a pretty slam dunk way to get a warrant.
When our current car dies, I’d like to replace it with an EV - but 0% chance it’ll be a Tesla.
What kind of curling issue, and did the Hilbert curve help with that?
I’ve found that I’m rarely doing something where my top layer lines matter. Usually, I get my finished surface by printing things face down on a textured sheet. This works for probably 95% of the things I print whereki care about finish. The others I’ll turn on ironing, but that’s probably way slower than the Hilbert curve.
We have a Bluetooth adapter for our car audio and it’s great. Plugs into the aux jack and car power. Really handy not needing to plug in.